What is 3D Metal Printing Technology?
Metal 3D printing is an ideal option for the manufacture of complex components that are difficult to machine. At lower volumes particularly, it can be a cost-effective alternative.
Harder metals such as stainless steel and titanium are harder to work and require better tools, more costly machines and generally greater costs. Thus, 3D printing is the preferred option depending on the job at hand and volume requirements.
One of the primary advantages with metal 3d printing is its capacity for use with an ever-growing list of alloys, metals and metallic composites, allowing for continual expansion and improvement of processes and ideas.
Additionally, there are other substantial benefits of producing metal parts with 3D printing instead of the usual techniques and technologies. These include:
Reduced lead times
One significant, well-known advantage of this type of ‘additive manufacturing’ is its faster turn-around time, from rudimentary design state to final part production.
This is a consequence of its design method - ordinarily, no specific tools or machining devices are needed for processing after the part has been printed.
No milling or turning is required for shape adjustment as with traditional techniques, it is only necessary to remove elements, such as any support structures, created during the process.
This reduction in steps allows for a significant decrease in post-processing times.
Cost advantages through reduced material waste
Another great advantage is a reduction in material waste. In the case of metal 3D printing, the raw materials are added and created in a layer by layer formation, instead of being subtracted or cut out of an original solid bulk.
In this way, the material is used only where needed and the cost outlay of the material used to produce one component is largely reduced.
Recent advancements such as Electron Beam Melting (EBM) and Selective Laser Melting (SLM) have allowed the introduction of powdered metal as a manufacturing option, and this has proven to be a giant leap forward in the industry.
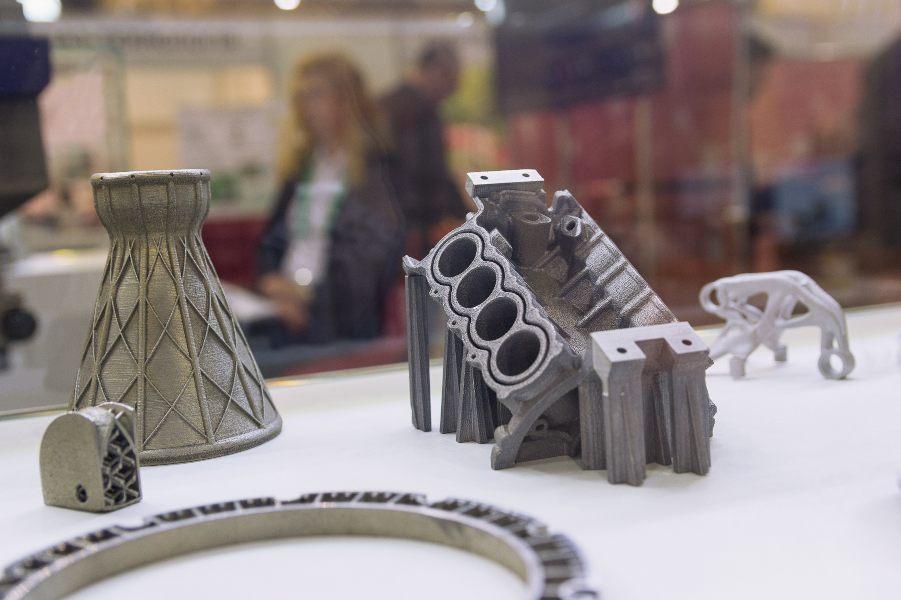
[Above: 3D Metal Samples]
3D Printing Metal Powder
Metal powders are metals that have been ground into fine particles and are the preliminary base element for most 3D printing processes that create metallic parts.
3D printing, or ‘additive manufacturing’ is the building of parts and components layer by layer.
The properties of the metal powder and the type of the 3D printing method determine the characteristics of the end product.
Metal powders are produced using several techniques, such as solid-state reduction, chemical processing, electrolysis, milling, and atomisation.
The most abundant of these methods is atomisation, as it produces the most geometrically usable powders for 3D printing.
Atomisation is usually created by one of three different techniques:
- water atomisation
- plasma atomisation
- gas atomisation.
In the case of 3D Printing, however, water atomisation is usually not used as it can produce irregularities not suitable for this style of manufacturing.
Plasma Atomisation
In this instance, the feedstock is introduced into the atomisation chamber in two possible forms, powder or wire.
In the chamber, a combination of co-axial plasma torches and gas jets melt and atomise the material, creating finitely round powder particles with a relatively finer size distribution.
Titanium is commonly produced this way.
There is a more specialised method called plasma rotating electrode process (PREP) and this utilises a rotating bar instead of a wire as the feed method.
In PREP, the bar extremity is melted at the entry point of the atomisation chamber by plasma torches, and the residual discharged melt becomes solid before reaching the housing walls.
This process creates powders of high purity, extreme roundness, and very fine particle sizes.
Gas Atomisation
In gas atomisation, a feedstock alloy is used, usually in ingot form, and melted in a furnace.
Ordinarily, a vacuum induced melting (VIM) furnace to monitor interstitial elements is used.
The furnace is aligned above the atomisation chamber to discharge material directly into the atomiser.
As this ‘melt’ channels through the chamber, high-pressure gas jets are utilised to atomise the material, which becomes solid spherical powder particles, and is then collected at the bottom.
Usually, this employs an inert gas, such as argon or nitrogen, to lessen oxidation and the possibility of contamination, but air can also be used.
The distribution of particle size can be modulated by adjusting the ratio of gas to melt flow rate.
Some powder materials producible by gas atomisation are cobalt, nickel, iron and aluminium.
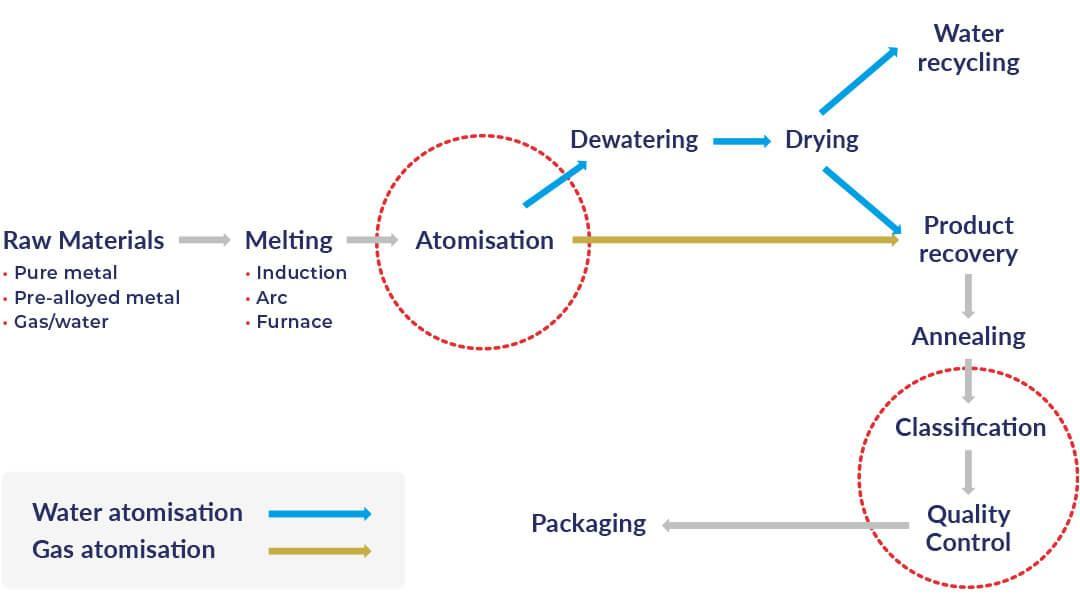
[Above: The Powder Atomisation Process]