Alloy Designations
- ISO composition: CuNi15Sn8
- European standards: EN 12163/CW355H
- UNS: C72900
- ASTM/AMS ASTM B 505 - AMS 4596, AMS 4597, AM 4598
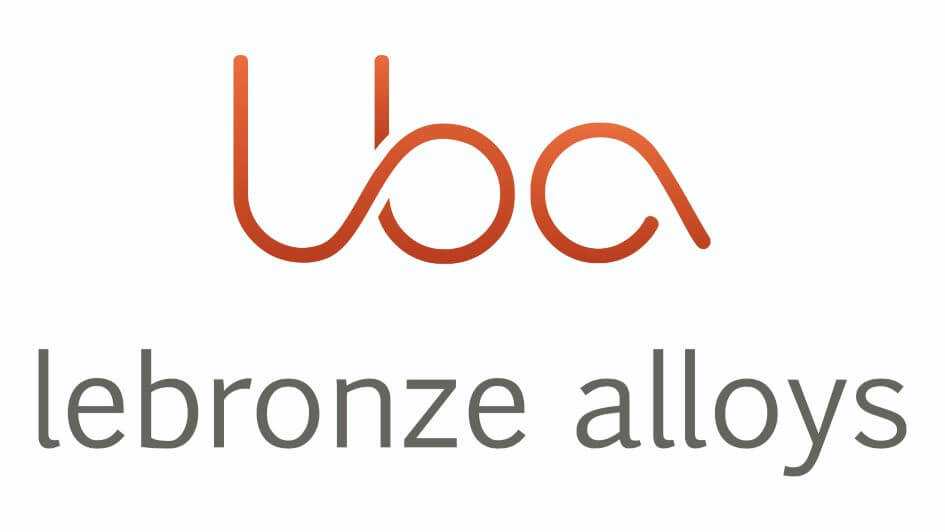
Hardiall® is manufactured by Lebronze alloys in an entirely integrated process, is a wrought and spinodally hardened alloy of copper, nickel, and and tin (CuNi15Sn8 / C72900). It has been developed with the express intent of delivering where high strength and toughness is demanded. Designed to be as resistant as possible to mechanical wear and abrasion such as galling and stress relaxation, as well as corrosion and erosion, Hardiall® is the go-to for many components where failure is not an option. Despite its toughness and dimensional stability within a huge range of temperatures (-125°C to 300°C), Hardiall® can still be formed into complex structures with ease. On top of all that, being free from lead or beryllium, Hardiall® is environmentally friendly.
Developed for the same applications as Toughmet® 3, Hardiall® has a proven track record in consistent performance and reliability. Being demonstrably and fully compliant with all relevant industry specifications and standards through extensive testing means Hardiall® is an ideal product to remove supply chain risks in high-end manufacturing industries.
As the entire manufacturing process used by Lebronze alloys for Hardiall® is integrated from beginning to end (from casting, through hot and cold working stage, to heat treatment and non-destructive quality testing), you can be sure of that the product meets all specifications. This integrated process also ensures complete traceability of the product.
Hardiall® is increasingly being used in a wide range of industries where thanks to the unique combination of properties it is helping to prevent failures and ensure a longer lifespan compared to traditional materials. Industries include motorsport, aerospace, oil & gas, construction, mining & heavy transport, automotive, defence, space, marine, power transmission and renewable energy.
Hardiall®is used within the aerospace industry thanks to its outstanding physical and mechanical properties in many varied components. Lebronze alloys has developed a full range of Hardiall®products matching the stringent needs of the aerospace industry.
In landing gear, bushings and bearings operate under severe conditions. They need to be lubricated and replaced frequently resulting in recurring maintenance downtime.
To reduce maintenance costs, Hardiall® is used for such applications as it demonstrates excellent lubricity, wear, and galling resistance, thus providing a longer service life and an improved total cost of ownership (TCO) compared to other copper and non-copper alloy materials.
Hardiall® is ideal for applications where the load required exceeds the performance of copper- nickel-aluminium based alloys or where lubricity is critical and titanium cannot satisfy the engineer’s requirements.
Hardiall® is used within the oil & gas industry thanks to its outstanding physical and mechanical properties in many varied components. Lebronze alloys has developed a full range of Hardiall® products to match the stringent demands of the oil & gas industry.
Hardiall® is used in bushings and bearings for drilling components. For such applications, Hardiall demonstrates outstanding wear, corrosion, temperature and pressure resistance, thus providing a longer service life and a better total cost of ownership (TCO) compared to beryllium copper, as well as some nickel or cobalt based alloys.
Hardiall®can be used in both offshore and onshore systems and in vertical or directional drilling products.
Hardiall® is also used in onshore oil pumps for sucker rod and valve rod guide bushing couplings. In such applications, where stainless steel is generally used, Hardiall®demonstrates excellent resistance to metal-to-metal wear, providing a reduction of failures.
Hardiall® is used within the mining industry thanks to its outstanding physical and mechanical properties in many varied components. Lebronze alloys has developed a full range of Hardiall® products to match the stringent demands of the mining industry.
In mining equipment, bushings and bearings are subject to extreme conditions and need to be lubricated and replaced frequently, which results in downtime and maintenance man-hours.
Hardiall® is used in excavators, mining trucks and longwall shearers, where its performance characteristics - lubricity, wear and galling resistance - make it the ideal material for bushings and bearings. In such applications, Hardiall® outperforms steel and manganese bronze due to its superior durability and reliability, reducing downtime and maintenance cost.
Motorsports are at the forefront of innovation and compared to conventional materials, Hardiall® enhances design optimization, with reduced mechanical clearances. It boosts performance and reliability and is mainly used in powertrain, steering and braking systems.
Hardiall®is used within industrial applications thanks to its outstanding physical and mechanical properties in many varied components. Lebronze alloys has developed a full range of Hardiall®products to match the variety of requirements for demanding industrial applications.
Hardiall® is used in bushings, bearings, worm & worm wheels and wheel shafts. For such applications, Hardiall® demonstrates outstanding mechanical strength and wear, corrosion and temperature resistance. Hardiall® contributes to longer service life and a better total cost of ownership (TCO) compared to steels, aluminium and phosphor bronzes.
Hardiall® is suitable for wear related parts like bushings and bearings in heavy metallurgical equipment like extrusion presses, rolling and drawing mills. In such applications where hardening steels, carbon steels or phosphor bronzes are generally used, Hardiall® demonstrates excellent resistance to metal-to-metal wear, thus providing fewer failures and hence reducing costly maintenance downtime.
High pressure equipment including:
Property | Value | Unit |
---|---|---|
Electrical Conductivity at 20oC (68oF) | 7.5 | % IACS |
Thermal Conductivity at 20oC to 200oC (68oF to 392oF) | 38 (22) | W/m/oC (Btu/ft/hr/oF) |
Coefficient of Thermal Expansion at 20oC to 200oC (68oF to 392oF) | 16.4 x 10-6 (9.1 x 10-6) | Per oC (Per oF) |
Density | 8.95 (0.323) | g/cm3 (lb/in3) |
Hardiall® is supplied peeled, with no mill scale and is up to 3% in supplied weight lighter, which gives up front material cost savings and negates the need for a descale machining operation. Standard Tolerance is + 1mm/- Nil
Hardiall® provides a longer lifespan to components minimising maintenance time and associated costs.Thanks to its high reliability it prevents unpredicted breaking events avoiding downtime.
Experienced multi-product specialists
In-house state of the art processing facilities
Large fleet of bespoke delivery vehicles
Value-added services provider
Standard, non-standard and customer-specific material
Opening Times
Experienced multi-product specialists
In-house state of the art processing facilities
Large fleet of bespoke delivery vehicles
Opening Times