Properties & Applications of Aluminium
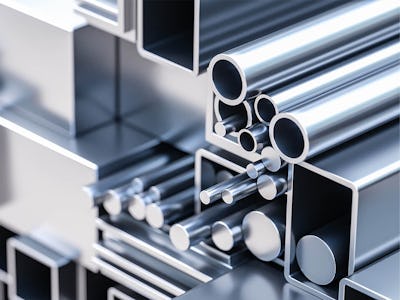
As a relatively new material, having only been commercially available since 1886, aluminium has undergone rapid development, evolving from a decorative material with very limited properties to a fully-fledged engineering material. Today, aluminium is used widely across a variety of markets and applications. Recent technological advancements, such as aluminium cutting/profiling and pre-machining of plate and bar, help deliver more efficient and cost-effective solutions for customers
Aluminium is available in a wide range of alloys, as well as multiple production processes and heat treatments. With its renowned corrosion resistance, good strength-to-weight ratio, and affordable abundance, aluminium has a wide range of applications.
These can be divided into two main categories of wrought alloy as listed below:
Heat treatable aluminium alloys consist of pure aluminium that is heated to a certain point. The alloy elements are then homogeneously added as the aluminium takes on a solid form. This heated aluminium is then quenched as the cooling atoms of the alloy elements are frozen into place.
In heat-treatable alloys, ‘strain hardening’ not only enhances the strengths achieved by precipitation but also increases the reaction to precipitation hardening. Work hardening is used liberally to produce strain-hardened tempers of the non-heat-treatable alloys.
Commercially pure aluminium also has a four-digit numerical identifier. Series 1xxx alloys are made of 99 percent or higher purity aluminium. Non heat-treatable.
The principal alloying element in the 2xxx series is copper. Heat treating these alloys improves their strength. These alloys are strong and tough, but not as corrosion resistant as other aluminum alloys, so they are usually painted or coated for use. The most common aircraft alloy is 2024. Alloy 2024-T351 is among the hardest of the aluminum alloys. Heat treatable.
The main alloying element in the 3xxx series is manganese, usually with a smaller amount of magnesium. The most popular alloy from this series is 3003, which is workable and moderately strong. 3003 is used to make cooking utensils. Alloy 3004 is one of the alloys used to make aluminum cans for beverages. Non heat-treatable.
Silicon is added to aluminium to make 4xxx alloys. This lowers the melting point of the metal without making it brittle. This series is used to make welding wire. Alloy 4043 is used to make filler alloys for welding cars and structural elements. Non heat-treatable.
5000 series aluminium is alloyed with magnesium, is readily weldable and used in a wide variety of applications including pressurised vessels, buildings and automotive. The alloy is not suitable for use in elevated temperature service.
Containing manganese and silicon, 6000 series aluminium's structure allows the alloy to be solution heat-treated which improves the strength of the material. The alloy is used in welding fabrication and to produce structural components.
7000 series aluminium is alloyed with zinc and can be precipitation hardened to provide the highest strength of all commercially available aluminium. This range of aluminium is used in industries such as aerospace and motorsport.
Sheet is how we best know aluminium and is found in all the major markets and industries.
As a packaging resource, sheet is often used to manufacture drinks cans, food cartons and foil.
While in the automotive and transport industries, aluminium sheet can be used to create panels for vehicle bodies and trailers.
Aluminium is ideally suited for items around the home due to its excellent thermal conductivity and being both lightweight and sturdy.
Aluminium plate is the heavy-lifter of the aluminium catalogue and can be applied to various industries, notably marine, aerospace and defence, where its use can be seen in key elements such as forming the skin of jets and spacecraft fuel tanks.
As a material, it is ideally suited for storage tanks, because some aluminium alloys become tougher at super-cold temperatures.
Aluminium plate is often used extensively in the marine industry, as a result of its weight advantages. Aluminium is around one third the weight of steel and therefore many in the marine architecture and construction industries have looked to aluminium panels for the manufacture of hulls in high-speed vessels such as catamarans and hovercraft.
Its weight advantage, coupled with its high corrosion resistance has also seen it become the metal of choice in the power generation industries, such as creating lighter and more durable elements of offshore oil rigs
Aluminium tubing is in high demand in a variety of trades, including air travel and rail transport. Its rare combination of lightness, flexibility and toughness make it ideal for fuselage, hydraulic systems, and fuel lines, and its heat conductive capabilities make it a great alternative to steel or other heavier metals in items such as refrigerators, engines and HVAC (heating, ventilation and air conditioning) systems.
It is also a superb solution for architecture and infrastructure projects, where corrosion resistance and the requirement for a lightweight material are the primary concern.
Aluminium rod and bar can be created by several different methods, including extrusion, rolling and coiling, or drawn directly from a molten aluminium core.
The application of these methods stretches the aluminium into either bar-shaped or circular pieces that can then be machined to a Pre-designed specification.
Aluminium ‘angles’ can be small or large, and are predominantly shaped blocks used to cover chipped edges, hide gaps, create borders and replace screw holes, and a host of other uses. They disguise the damaged surface behind the silver body. By the same token, they can also be used to hide rough, uneven surfaces that are not able to be easily smoothed over.
Tube Steel or ‘Box Section’ is how we refer to Square and Rectangular HSS (Hollow Structural Section). A metal profile type with a hollowed-out cross-section, often used in construction and plumbing industries due to its corrosion resistance and low tensile strength, therefore it is ideal as an alloy when linked with silicon, copper, manganese, zinc and many other metals.
Aluminium extrusion is widely used throughout a variety of industries.
Extrusions provide ideal solutions for a vast range of equipment and machinery. Lightweight, high-strength, low maintenance and the ability to create intricate shapes make extrusions a key component in today's manufacturing processes.
A high powered ram flushes aluminium through a die and it is forced out of the die opening. This results in it coming out in the same shape as the die which is then pulled out along a runout table.
A runout table is a device or ‘table’ designed to hold a pipe or tube after it has been cut to the desired length, it is then transferred to another holding area.
At a primary level, this process is quite simple to understand. It's a similar mechanism to what happens when you squeeze a tube of toothpaste with your fingers - the toothpaste comes out in the shape of the opening, this opening serves the same function as an extrusion die. Since the opening is a solid circle, the squeezed Aluminium will come out as a long extrusion.
‘Machining’ is what's known as a subtractive manufacturing process, meaning it removes material from a central design block, or ‘workpiece’ to create the desired part or product. It is a highly versatile process applicable to a whole host of metal and non-metal substances. Aluminium is one of the most widely used ‘machined’ materials available today.
‘Pre-Machining’ is a process where a roughing operation is used to remove significant amounts of material quickly and to produce a part-geometry close to the desired shape.
Both of these above methods allow mass-producible central models from which varying products on a theme can be created, the end effect being that aluminium projects can be completed in a much faster and cost-sensitive way.
Experienced multi-product specialists
In-house state of the art processing facilities
Large fleet of bespoke delivery vehicles
Value-added services provider
Standard, non-standard and customer-specific material
Opening Times
Experienced multi-product specialists
In-house state of the art processing facilities
Large fleet of bespoke delivery vehicles
Opening Times