Grades
Your search did not match any items. Please ensure all words are spelled correctly or try different / more general keywords.
Sign & Display
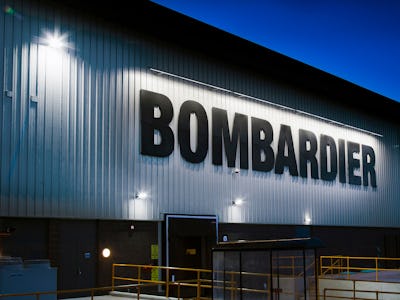
Marine & Shipbuilding
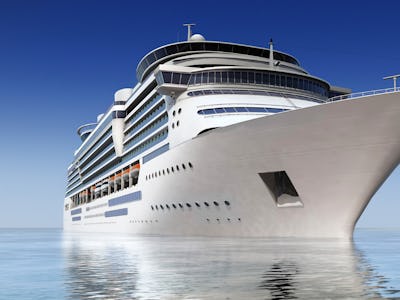
Automotive & Transportation
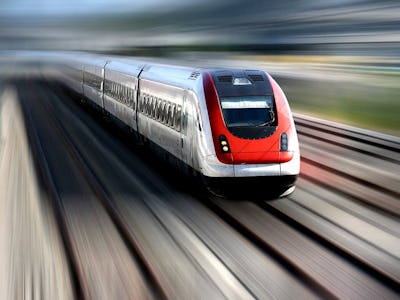
Architecture & Infrastructure
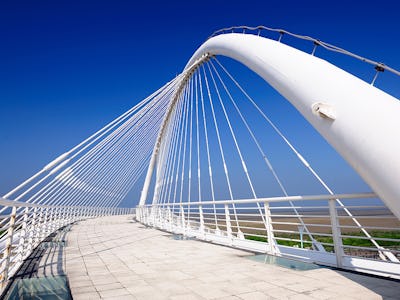
General Information for PVC
PVC Properties
PVC is highly versatile and cost-effective. Its main benefits and uses include:
- Durability: PVC is resistant to weather, shock, abrasion, corrosion, and chemical erosion. This makes it ideal for many outdoor and long-life products.
- Excellent Mechanical Properties: PVC is lightweight, tough and resistant to scratches and abrasions.
- Insulating: Thanks to high dielectric strength, PVC is a great choice for electric and electronic insulations.
- Cost-effectiveness: Low maintenance and longevity are two standout qualities of PVC, making it a superb cost-effective choice compared to other materials.
- Flame Retardancy: Containing high levels of chlorine, PVC is self-extinguishing. An organic compound used in PVC, antimony trioxide is used extensively, commonly in conjunction with phosphate ester plasticizers to provide outstanding fire performance.
- Chemical resistance: PVC is highly resistant to inorganic chemicals such as diluted acids, diluted alkalis and aliphatic hydrocarbons. It is however attacked by ketones, esters, chlorinated and aromatic hydrocarbons, and some aromatic ethers and amines. This leads to swelling and a reduction in tensile strength.
History of PVC
The first example of PVC was created by the French chemist Henri Victor Regnault in 1835, and then further investigated by the German chemist Eugen Baumann in 1872.
It was not until 1912, while testing vinyl chloride polymerisation by means of sunlight, that another German chemist Friedrich Heinrich August Klatte had created a commercially viable form of PVC.
It was quickly patented and though used by many industries, it was still limited by being somewhat inflexible.
This was until 1926 when Waldo Lunsbury Semon of the Goodrich Company in the U.S. produced what we now call ‘plasticised PVC’, a pliable and inert version of the previously much-lauded but limited PVC product.
This discovery made commercial success a certainty and Goodrich began creating shock-absorber seals, coated cloth products and electrical wiring insulation.
From there it has expanded and the uses and applications of PVC continue to grow with the needs of our technological times.
Today it is found throughout industry and is one of the pacesetters of technological evolution.
PVC Production
The natural raw materials for PVC are taken from salt and oil.
Electrolysis of saltwater produces chlorine, which is mixed with ethylene (obtained from oil) to form a vinyl chloride monomer, known as VCM.
Molecules of VCM are polymerised to form PVC resin, and then additional additives are added to make a customised PVC compound.
Making PVC is a 5 Step Process:
- Salt and Hydrocarbons are extracted.
- Ethylene and Chlorine are produced from the extracted components.
- Combined, these make a vinyl chloride monomer
- This monomer is then polymerised to make PVC
- PVC is blended with various materials to create differing physical properties.
PVC Sustainability
Manufacturing PVC uses up less non-renewable fossil fuel than any other commodity plastics.
PVC is a thermoplastic as opposed to a thermoset plastic, which means it becomes liquid at melting point so can be reused time and again.
Thermoset plastics will instead burn, meaning new raw materials need to be used each time, draining important natural resources.