Grades
Your search did not match any items. Please ensure all words are spelled correctly or try different / more general keywords.
Sign & Display
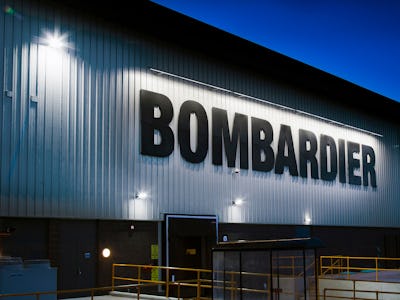
Marine & Shipbuilding
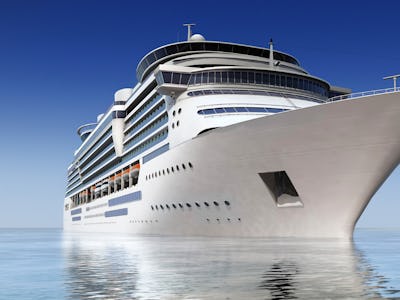
General Information for Polycarbonate
Polycarbonate Products
Flat Polycarbonate Sheet
Flat polycarbonate is available in a range of tints, colours and finishes that offer different levels of light transmission and light diffusion depending on design requirements.
Clear sheet provides high optical clarity, making it the ideal glazing option for those applications that require high levels of light transmission.
Depending on sheet thickness, clear flat polycarbonate sheet offers exceptional light transmissions of between 80% and 92%.
It is also available in tinted options including bronze, opal, green, blue and grey offering varying degrees of solar control, resulting in cooler internal environments.
Whilst solar transmission is reduced, the sheet continues to transmit free natural light, reducing the need for artificial light, helping reduce energy costs and the associated CO2 emissions.
The weight of flat polycarbonate is only half that of plate glass, making handling and installation much more convenient.
The strength and rigidity of polycarbonate sheet enhance the spanning capability, making the sheet self-supporting, resulting in reduced requirements for support structures and increased resource efficiency.
The material is extremely practical and can be cut on-site to the required shape or size, minimizing waste.
Flat polycarbonate sheet provides excellent design flexibility. It can be cut, cold curved or thermoformed, without losing impact strength or durability, enabling the designer to create interesting glazing solutions for a bright naturally lit interior environment. It is the ideal glazing solution for covered walkways, canopies, skylights, domes, bus shelters and train windows.
In addition to this it can be screen printed directly and the smooth and even surface makes it ideal for vinyl adhesion.
It has substantial bonding compatibility and its resistance to knocks and scratches makes it perfect for use in high traffic areas and applications including signs, point of sale and store fixtures.
Clear sheet provides high optical clarity, making it the ideal glazing option for those applications that require high levels of light transmission.
Longlife Polycarbonate Sheet
Protection against harmful UV radiation
Longlife polycarbonate features a co-extruded UV protection on both sides of the sheet cutting out 98% of the harmful UV radiation, making it the ideal product for use in some of the worlds’ toughest climate conditions.
The UV protective layer enables longer sheet life expectancy, prevents yellowing and guards against loss of strength.
Combine this with high impact and chemical resistance, lightweight and high light transmission, and longlife polycarbonate is the superior glazing material for architectural rooflights, vertical glazing and specialist glazing applications.
Abrasion Resistant Polycarbonate
With strength 200 times greater than glass, it is virtually unbreakable.
Abrasion-resistant polycarbonate is an extruded polycarbonate flat sheet combined with abrasion and chemically resistant coating.
The highly resilient and abrasion-resistant surface coating resists marks and scratches, vandalism, graffiti and physical attack and also withstands contact from a wide range of cleaning agents, organic solvents and corrosive elements.
Abrasion-resistant polycarbonate offers superior toughness for those areas where high performance and reliability are essential whilst providing high natural light transmission.
Combined with its shatter and splinter resistance it is much safer than glass, making it the ideal safety glazing solution for high traffic areas including bus stops, traffic signage, commercial glazing, schools and other public and commercial areas.
Mirrored Polycarbonate
Polycarbonate mirror sheet is intended for areas at high risk from impact such as prisons, horse stables, hospitals or similar risk environments, where the significantly improved impact strength over the standard acrylic mirror is a design essential.
Polycarbonate mirror is virtually unbreakable, with an impact strength of around 30 times that of its acrylic counterpart, and over 250 times greater than that of glass of equal sheet thickness.
It is a standout product for use in thousands of products thanks to its ease of fabrication, low heat loss and attractive clear edge colour.
From point-of-sale displays to signage, lighting and dozens of other applications, a Polycarbonate mirror sheet is an ideal design solution.
Polycarbonate Properties
Widely used in the industry for its versatile properties, eco-friendly potential and recyclability, polycarbonates' unique set of chemical and material properties make it a suitable replacement for glass, PMMA and PE.
- Tough: Maintains toughness up to 140℃ and down to -20℃. Polycarbonate is also virtually unbreakable and abrasion-resistant
- Transmittance: An extremely clear material polycarbonate can transmit over 90% of light. Polycarbonate also offers fantastic optical properties with a refractive index of 1.584.
- UV Protective: Polycarbonate can be designed to block 100% of ultraviolet radiation.
- Lightweight: Despite being 200 x stronger than glass, polycarbonate is half the weight. Its low weight makes it easy to install and transport.
- Chemical Resistance: Good chemical resistance against diluted acids, alcohols and aliphatic hydrocarbons. Important to note though that the material can be readily attacked by diluted alkalis, aromatic and halogenated hydrocarbons, so it must be cleaned with agents that do not affect its properties.
- Heat Resistance: Naturally thermally stable up to 135℃, further heat resistance can be achieved by adding flame retardant elements without affecting its properties.
- Excellent in water and temperature environments
- Good electrical insulation
- Resistance to steam sterilisation
- Efficiency over other thermoplastics
Polycarbonate Industry Applications
Automotive/Transportation
Polycarbonate has superb rigidity and excellent creep resistance, this makes it ideal for interior and exterior design.
Being tough, lightweight, transparent, easily coloured and durable make it both eye-catching and resilient, and an ideal choice for the car industry.
Electrical Appliances
Being easy to shape and curve polycarbonates and their blends are a top choice for refrigerators, coffee machines, washing machines, food mixers and a host of other household appliances.
Food Contact
With high levels of heat resistance and shatter resistance, as well as being readily re-usable, polycarbonate is ideal for direct food and beverage containers.
Building & Construction
Used as an alternative to glass it is ideal in the construction industry where safety is a required element.
Its properties of transparency, weatherability and high impact strength are highly valued and sought after.
Applications include agricultural housing, security windows, shelters, skylights, public buildings
3D Printing
Polycarbonate is the strongest thermoplastic material and an excellent choice for 3D printing filaments.
PC is also temperature resistant and has high material strength meaning it is less likely to shatter like other materials such as plexiglass.
Consumer Products
Being both transparent and tough, it is an ideal choice for many objects, among these are shatterproof sunglasses, industrial water bottles, safety goggles, face shields, and it is also a critical component of bulletproof glass.
It has also long been used for producing CDs and DVDs.
Electrical & Electronic
Noted for its strength, polycarbonate is an ideal material for protective housing for switches, circuit breakers, plugs, sockets, switchgears, relays and other electrical components.
And polycarbonate films help to prevent scratching on screens.
Medical
With high levels of dimensional stability, toughness and heat resistance, polycarbonate has excellent characteristics for use in medical supplies and equipment.
Common applications include surgical instruments, blood reservoirs, blood filters, hemodialysis membranes and drug delivery systems, all areas previously served by glass or metal but now superseded by polycarbonate.
Polycarbonate Processing Methods
Injection Moulding
Injection moulding is the most common method to produce parts made from polycarbonates and their blends.
During injection moulding, a hot polymer melt is pushed through a mould at high pressure. This mould is then allowed to cool and solidify into the desired shape and style.
In polycarbonates, this method is used to create bottles and plates, as well as countless other products we use today.
It is essential that the wall thickness isn't too thin as polycarbonate is a poor flowing plastic.
Extrusion
Through extrusion, the polymer melt is passed through a specially shaped cavity or ‘die’. This is then allowed to cool and solidify maintaining this desired shape.
In polycarbonates, this method is used in the manufacture of polycarbonate sheeting, pipes and design profiles.
Polycarbonate & Food Contact
Many of the world’s top regulatory authorities, such as US FDA, European Commission's Scientific Committee on Food, UK Food Standards Agency, have recognized polycarbonate as safe for use in food contact applications. However there are some studies as well which showed BPA to be hazardous to health and so, polycarbonate products are often now ‘BPA free’.
Polycarbonate Sustainability
Polycarbonate is a sound choice when it comes to recycling, because its thermoplastic.
Thermoplastics (as opposed to thermoset plastics) become liquid at melting point so can be reused time and again.
Thermoset plastics will instead burn, meaning new raw materials need to be used each time, draining important natural resources.