Grades
Your search did not match any items. Please ensure all words are spelled correctly or try different / more general keywords.
Automotive & Transportation
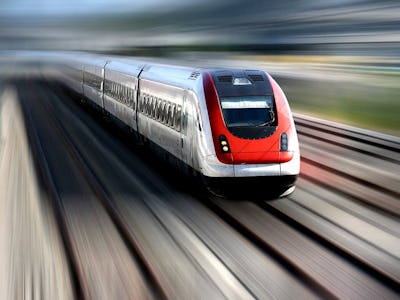
Precision Engineering
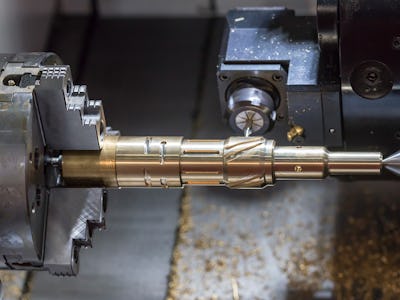
General Information for Engineering Plastics
Engineering Plastics Industry Applications
Engineering plastics can be found in many industries and applications including:
- Building
- Construction
- Consumer goods and appliances
- Automotive
- Industrial
- Mechanical Engineering
- Food
- Pharmaceuticals
- Aerospace
- Medical technology
- Transport
These days, engineering plastics can effectively replace metals or ceramics in many instances. Moreover, they are the best and most suitable choice for unusual and intricately shaped applications or parts.
This makes them a highly sought after material for many businesses with very exacting project specifications.
When compared to the more widely used commodity packaging plastics such as polystyrene, polypropylene, polyethylene or PVC, engineering plastics show superior mechanical strength and thermal resistance, and are able to survive in temperatures up to 150° C.
Engineering Plastics Processing Methods
Engineering Plastic Extrusion
Extrusion is a temperature regulated, pressure-based process whereby the material is heated in an extrusion barrel through zones of increasing heat and then forced at pressure through a specially shaped die.
The resulting mould is often a semi-finished product that can then be further adapted to more exacting specifications, such as stock bars, tubes or plates in a variety of dimensions and colours.
Engineering Plastic Compounding
Compounding is a process where the raw material of the plastic is melted with fillers or additives. They are then extruded into thin strands and subsequently cut into granulated form.
This method allows the specific plastic to be adapted to unique specifications or design requirements, such as enhancing frictional ability or increasing electrical conductivity.
Engineering Plastic Injection Moulding
Used in mass manufacturing, injection moulding is a process used when ready-to-go finished products are needed.
The plastic is melted by an extruder, plasticized and then injected at pressure into an injection moulding tool. This ‘tool’ has various cavities and shapes and determines the desired shape and surface structure of the finished component.
It is a more expensive process and is therefore only usually applied for mass production.
Engineering Plastic Compression Moulding/Sintering
Used to produce semi-finished moulds and custom castings, compression moulding and sintering create products with a minimal likelihood of warping.
Using powdered particles pressed at very high temperature into a mould, this method is labour intensive and costly and rarely used.
Cast Polyamide
This ‘pressureless’ custom casting method has been shown to be particularly effective when producing thick-walled components. Usually, these are ‘almost finished’ products that can then be designed to order.
Able to create rods, plates, tubes with substantially larger dimensions than the extrusion method, but cast polyamide products do have a lower intrinsic stress level than extruded components.
Machining
Machining is the most common, fastest and most cost-effective way to arrive at a finished product.
Through machining, finished parts with extremely close tolerances are produced from engineering and high-temperature plastics.
Machining involves the use of CNC milling machines, lathes and saws which are fitted with special tools to shape and design the desired product form. This is really the shaping stage once the stock shape or injection moulded part has already been produced.
Engineering Plastics Sustainability
Engineering plastics are a sustainable and reproducible product, known as a thermo-plastic. They don’t burn at high temperatures like many other plastic alternatives.
They instead become liquid and as such can be remoulded and reused infinitely, lessening the global impact on natural resources, and making them a sound, energy-conscious choice.