Anti-Bacterial & Anti-Microbial Uses for Copper & Copper Alloys
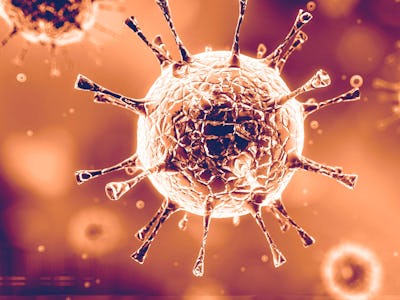
One of the most tarnish resistant of all the copper alloys, the appearance aluminium bronze does not deteriorate when exposed to the effects of atmospheric corrosion.
Used primarily in subsea environments, aluminium bronzes are increasingly being used in a variety of markets including chemical and petrochemical plants, power generation (including nuclear), desalination plants, aircraft and automotive engineering, marine and offshore, building and construction and general engineering.
Righton Blackburns extensive and diverse stock, coupled with our on-hand technical experts mean we should be your go-to aluminium bronze supplier.
Your search did not match any items. Please ensure all words are spelled correctly or try different / more general keywords.
The four major groups of Aluminium Bronze are:
Primarily noted for high tensile strength, wear resistance and superb corrosion characteristics, aluminium bBronze sheet is most often used for heavy loads where corrosion resistance and susceptibility to wear are significant factors.
Aluminium bronze bars or (rods) are fantastic heat and electricity conductors. They are also tough, durable and superbly corrosion resistant allowing for multiple applications throughout many industries.
High strength, corrosion resistant and resistant to wearing, aluminium bronze plates are commonly used for heavy loads in corrosive and friction based environments
Using forged aluminium bronze is a way of ensuring a superior tensile strength to other metals including cast iron, zinc or aluminium.
Best used where materially dense products are needed, forging is dimensionally accurate and present with a lustrous surface quality.
Centrifugally cast rings are formed when molten copper is poured into a spinning round mould.
This spinning action creates centrifugal force, which in turn creates pressure on the molten copper which then begins to solidify.
When poured the heavier metal elements are forced outwards, allowing the lighter oxides and any impurities to flow to the inside diameter, allowing them to be removed during the machining process.
Continuous casting is the process of feeding molten metal through a furnace. Through this casting method any dirt, gasses or grit rise to the top of the melt and are left behind.
The temperature is monitored to control the grain structure and properties of the resulting cast bronze. This continuous process prevents any shrinkage, cavities or dirt that would affect the purity of the metal
There are advantages of using continuous casting for aluminium bronze whether it be for solid or hollow parts including bar, tube and plate, as follows:
Aluminium bronzes are essentially copper-aluminium alloys with 5-11% aluminium. This is then mixed with other metal elements, such as iron, nickel, manganese and silicon, these are added in varying degrees to enhance the mechanical and physical properties.
Aluminium bronze castings have exceptional corrosion resistance, high strength, toughness and wear resistance and are great candidates for both casting and welding.
The benefits of aluminium bronze include:
Aluminium bronzes achieve the highest strength of all the copper-based alloys, with similar physical characteristics to mild steel.
They also have exceptional corrosion resistance, because the aluminium in the alloy reacts with oxygen in the atmosphere to form a thin, yet strong, surface layer of aluminium oxide. This aluminium oxide acts as a barrier to corrosion.
For this reason, aluminium bronze is widely used in marine and offshore environments for propellers, underwater fastenings, valves and pumps, as well as heavy duty applications like sleeve bearings, gears, fasteners, bushes and bearings
Another significant benefit for subsea use is the alloy’s biostatic effects in water – which means that it inhibits the growth of algae, lichen, mussels and barnacles. Ships hulls are often coated with aluminium bronze, helping to reduce maintenance costs and improve efficiency.
It is also the most tarnish resistant of all the copper alloys and the appearance of the material does not deteriorate when exposed to the effects of atmospheric corrosion.
Not just limited to marine application, aluminium bronzes are a go-to product in a growing variety of other diverse markets including chemical and petrochemical plants, Power generation (including nuclear), desalination plants, aircraft and automotive engineering, building and construction and general engineering.
In fact aluminium bronzes are the most widely used of all the high performance copper alloys, recognised as a versatile, high strength, corrosion resistant alloy.
Experienced multi-product specialists
In-house state of the art processing facilities
Large fleet of bespoke delivery vehicles
Value-added services provider
Standard, non-standard and customer-specific material
Opening Times
Experienced multi-product specialists
In-house state of the art processing facilities
Large fleet of bespoke delivery vehicles
Opening Times