Commercial Nickel Alloys
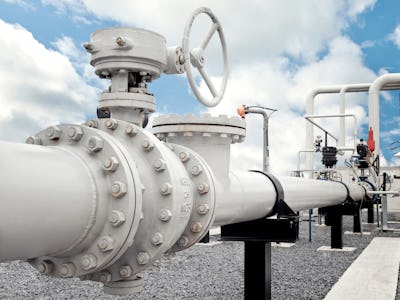
Nickel alloys give excellent performance over a wide range of temperatures, operating environments, and media - where strength and corrosion resistance are critical.
Marine engineering, chemical and petrochemical processing and the oil and gas industry all benefit from the use of these alloys in diverse components; from valves, through fasteners, to drill collars.
Righton Blackburns stocks a full range of nickel alloy products, including Alloy 400, 500, 625, 718, 800 825 & C276.
Grade | Applications |
---|---|
Nickel Alloy 20 | Sulphuric acid tanks and racks, heat exchangers, and the manufacture of solvents, organic chemicals, explosives, synthetic fibres and pharmaceuticals. |
Nickel Alloy 22 | Flue gas systems, pollution control, chemical processing, sour gas systems, waste incineration, pulp and paper processing. |
Nickel Alloy 36 | Liquified gas storage, strips for thermometers, composite wing moulds, laser components, thermostat rods. |
Nickel Alloy 41 | Aircraft engine parts such as nozzle partitions, wheels, turbine blades, combustion chamber lining. |
Nickel Alloy 86 | Heat treatment furnace equipment, afterburner parts, gas turbine combustion chambers. |
Nickel Alloy 188 | Gas turbines, flame holders, liners and transition ducts, combustion parts. |
Nickel Alloy 200 | One of the most widely used standard grades of commercially available pure wrought Nickel. It offers good thermal conductivity, mechanical strength and resistance against many corrosive environments, in particular against caustic alkalis. It also has low electrical resistivity and good magnetostrictive properties. Nickel 200 is easily workable by forming and drawing. Applications include: containers and piping, product purity in food handling, chemical processing and electronics. |
Nickel 201 | Nickel 201 is a low carbon variation of Ni200 and has a very low work hardening rate which allows it to be easily cold formed. It also offers better creep resistance and is preferred over Ni200 for applications that experience temperatures over 600°F (315°C). |
Nickel 205 | Nickel 205 is used for applications similar to those of Ni200, where higher purity and conductivity are required. Nickel 205 is produced by changing the composition of Ni200 chemistry. These alterations improve the properties needed for electrical and electronic applications. Applications include transistor housings, lead wires, anodes for electronic valves, and for making wire mesh and filters for chemical and petrochemical industry. |
Nickel Alloy 400 | Chemical and hydrocarbon processing, shafts, fasteners, heat exchangers, pumps, valves, fittings and marine equipment. |
Nickel Alloy 500 | Has around three times the yield strength and double the tensile strength in comparison to Nickel 400. Options to add aluminium and titanium, enable the alloy to be precipitation hardened. |
Nickel Alloy 600 | Heat treatment, furnaces, cooking appliances, chemical and food processing, nuclear engineering, sparking electrodes. |
Nickel Alloy 601 | Gas turbine components, heat treat baskets, industrial furnaces, petrochemical equipment. |
Nickel Alloy 617 | Gas turbines for combustion cans, ducting, transition liners, petrochemical processing, heat treating, nitric acid production. |
Nickel Alloy 625 | Chemical processing, oil and gas sour service flowlines, chemical injection lines, heat exchangers, aerospace, marine engineering, pollution control, nuclear reactors, wellhead equipment. |
Nickel Alloy 718 | Aircraft ducting and engine plumbing, rocket motors, spacecraft, nuclear reactors, pumps, tools, gas turbines. |
Nickel Alloy 800H | Process piping, heat treatment fixtures, furnace parts, superheater and reheater tubes in power plants, chemical and petrochemical processing. |
Nickel Alloy 800HT | Process piping, heat treatment fixtures, furnace parts, superheater and reheater tubes in power plants, chemical and petrochemical processing. |
Nickel Alloy 825 | Jet engine pods, parts and fasteners, pollution control, chemical processing, oil and gas well piping, nuclear fuel reprocessing acid production. |
Nickel Alloy C276 | Nickel alloy C-276 is a great candidate for most chemical and petrochemical processing applications when welded. It has excellent resistance to reducing acids, sulfuric acid, applications when welded. It has excellent resistance to reducing acids, sulfuric acid, hydrochloric acid, brine solutions, oxidizing chlorides, and hot seawater. It also has exceptional resistance to crevice corrosion and stress corrosion cracking, as well as chloride pitting, and its low carbon content lessens carbide precipitation during welding, preserving its excellent resistance to corrosion. This means that C-276 can be readily fabricated by welding using methods similar to those utilized for nickel-based alloys. |
Category | Description |
---|---|
Duranickel Alloys | Containing more than 94% nickel content, these Nickel Alloys have 4.75% manganese and are able to resist sulphur corrosion at high temperatures. Duranickel retains excellent properties up to 600°F. The corrosion resistance of these alloys is similar to that of commercially pure wrought nickel. |
Nickel-molybdenum (Ni-Mo) and nickel-molybdenum-chromium (Ni-Mo-Cr) Alloys | Alloys in this group are used for high strength performance in extremely high temperatures and corrosive surroundings. Hastelloy B is highly prized for its Hydrogen Chloride resistance and for its creep and rupture strength at temperatures around 1,400°F. |
Nickel-molybdenum-chromium-copper (Ni-Mo-Cr-CU) Ilium Alloys | These alloys, which are mostly in cast form, are most noted for their corrosion resistance. Wrought illium for example works extremely well in seawater. Illium B, a cast alloy, is highly resistant to sulphuric acid. Illium 98 is a cast alloy with much more resistance to corrosion than ilium G. Illium G is a weldable wrought alloy, able to resist hot sulphuric acid and phosphoric acid. |
High Nickel Alloys & Superalloys | These nickel copper alloys are sometimes referred to as NiCu and contain nickel with copper and small amounts of iron and manganese. A typical nickel copper alloy is the 400 grade, containing 63% nickel minimum, 28-34% copper, and a maximum of 2% manganese and 2.5% iron. |
Nickel Copper Alloys | These nickel copper alloys are sometimes referred to as NiCu and contain nickel with copper and small amounts of iron and manganese. A typical nickel copper alloy is the 400 grade, containing 63% nickel minimum, 28-34% copper, and a maximum of 2% manganese and 2.5% iron. Nickel copper alloys have higher strength values than pure nickel and have a wider range of environmental corrosion-resistant uses but in some specialised applications, such as strong alkali contaminant, ‘commercially’ pure nickel would often be superior. Nickel copper alloys have wide and varied applications in oil refining and marine applications where long term corrosion resistance is essential. Because of their excellent thermal conductivity, they are often used for heat exchangers to combat the impacts of seawater. The most used of these alloys are Monel 400, Monel R-405, and Monel K-500. The K-500 version can be precipitation hardened to high levels of strength much like Duranickel. These alloys are easy to form and have a wide range of mechanical properties, and high corrosion resistance. They are strong and tough at sub-zero temperatures and perform well for stress-corrosion cracking. K-500, however, does show a tendency to stress-corrosion cracking when precipitation hardened. Note: Cast Nickel Copper alloys containing 3 to 4% silicon have excellent non-galling and anti-seizing characteristics. |
Nickel Chromium Base Alloys | These alloys are used extensively in applications where resistance to heat and/or corrosion is needed. Many metals fail at high temperatures due to oxidation (scaling) or through a loss in strength. Alloys in this class are designed to resist both of these impacts. When corrosion resistance is the absolute priority, molybdenum is also used as an alloying element in addition to the chromium nickel alloy. Note: Nickel alloys are not suitable for high-temperature sulphur rich environments. |
Experienced multi-product specialists
In-house state of the art processing facilities
Large fleet of bespoke delivery vehicles
Value-added services provider
Standard, non-standard and customer-specific material
Opening Times
Experienced multi-product specialists
In-house state of the art processing facilities
Large fleet of bespoke delivery vehicles
Opening Times