Grades
Your search did not match any items. Please ensure all words are spelled correctly or try different / more general keywords.
Sign & Display
Righton Blackburns is a leading distributor to the sign, display and print markets supplying a comprehensive range of premium grade materials. From print sector digital grade substrates, to bespoke...
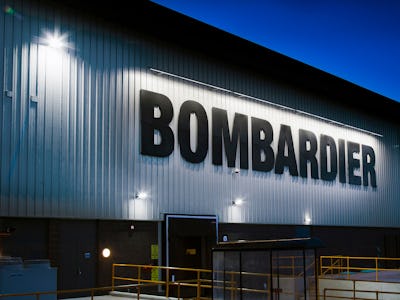
Marine & Shipbuilding
The first choice for quality and service, Righton Blackburns satisfies the diverse and exacting requirements for high strength and corrosion resistant material for all marine markets, including:...
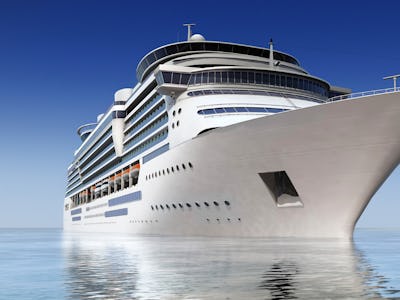
General Information for Acrylic
Acrylic Overview
Acrylic is a polymethylmethacrylate or PMMA.
It is a see-through thermoplastic homopolymer that has a host of different manufacturing processes.
Thermoplastic refers to how the plastic responds to heat, thermoplastics become liquid at their melting point (160 degrees Celsius for acrylic), allowing them to be reheated multiple times.
By contrast thermoset plastics cannot be heated at a high temperature twice, on the second attempt they would burn rather than liquify.
As an impact-resistant alternative to glass it has found a commercial foothold in many markets, creating products such as lenses, nails, medical devices, LCD screens, furniture, paint, bone implants, dentures, surrounds for hockey rinks, aquariums and so on.
The raw materials used to create acrylic allow for a superb level of light conversion so coloured or clear, it is a suitable and safe alternative to glass.
It is also a material in vast supply and inexpensive to manufacture giving it commercial superiority to other products in the plastics market.
One comparative downside is its lack of material strength compared to other plastics such as polycarbonate. Often in these instances acrylic will still be used, but as the scratch-resistant laminate on top of polycarbonate with its greater material strength.
Bullet resistant glass is often made this way.
Benefits of Acrylic include:
- Weathering and age resistance
- Suitability for food production and contact
- Easy fabrication
- Excellent optical properties
- Thermoformable
- Superb impact resistance
- Cost-effective
- Good electrical resistance
- Good UV resistance
- High-quality surface finish
It is the perfect choice for outside signage but can equally be applied to many internal usages such as POS and display features.
Acrylic Products
Cast Acrylic
Available as standard, in clear, opal, white and black. Cast acrylic is a perfect choice when a visual Impact is required. It is lighter than glass of the equivalent thickness and offers optical transparency (93% light transmission for clear), with a number of benefits such as high impact resistance, UV resistance, good thermal stability, low water absorption and perfect transparency for displays. In addition, it is easy to handle and is the ideal substrate for the following processes: Printing, laminating, sawing, drilling, thread cutting, milling, laser & water jet cutting, polishing, bonding, welding, hot bending, thermoforming and tempering. A wide range of colour options and speciality finishes are also available.
Our range of cast acrylic opals, available in all industry-standard tints and light transmissions, optimised for backlit lighting applications whilst also providing a clean, bright appearance during daylight hours when the product is not illuminated.
Extruded Acrylic
Extruded aacrylic is the most versatile of sheet materials. Its brilliant transparency and durability make it an excellent choice for applications where appearance is important. It has very good weathering and ageing resistance. Can be used in contact with foodstuff, it is easy to fabricate, with good optical properties and a high-quality surface finish.
Perfect for both outside signage and many internal usages such as POS and display features, it is available in a range of 6 different Opal tints to suit most needs, additionally, speciality coloured finishes are also available.
Mirrored Acrylic
Sparkling clarity and the ability to be formed into shapes makes extruded acrylic sheet the perfect material for any POS application.
The perfect material for many applications including POS, sign making, lettering, shop fittings, motor homes and refrigeration end panels. Available silver, gold, copper, bronze, grey, anthracite, in 2440 x 1220 x 3mm.
The History of Acrylic
Created back in 1843, acrylic acid was the base idea for all products that have followed since. By 1877 the first reports of an acrylic material began to emerge and it made its way onto the main commercial-stage around 50 years later when Herr DR Otto Rohm produced an Acrylic sheet for the first time through polymerisation that made it commercially viable.
Full factory production began in 1934 at the company Rohm & Haas in Darmstadt, Germany.
Soon after in 1935, a way to cast acrylic was created by the ICI company in the UK, where the first acrylic sheets were used for lenses, windows and various types of covering
Acrylic became a vitally important material in the Second World War due to its flexibility and visibility, (it was used for submarine periscopes, aeroplane windows, canopies and turrets) and was much less likely to shatter than glass.
Until this time ‘clear’ acrylic had been the primary focus, but it was after the war that its true versatility came to the fore.
Able to be easily formed with colour and diffusion (opal) a huge range of applications began to emerge including protective fluorescent lights, street light covers and illuminated advertising.
In fact, wherever a material had to be hard-wearing, lightweight, hard to break and weather-resistant, acrylic became a natural go-to product, and its range of uses and market applications grew exponentially.
In almost every country an acrylic company took root - These companies were often small family-run enterprises using acrylic sheets to make items such as buttons, combs and buckles with a ‘mother of pearl’ effect.
Prototype acrylics were now being tested by adding additives such as latex to make acrylic impact resistant.
Today its uses extend as far as aquarium walls and nail polish.
Acrylic Sustainability
Acrylic is a thermoplastic, and as such can be melted, cooled and reheated without any significant degradation. Instead of burning, thermoplastics liquefy, which allows them to be re-manufactured, as such, Acrylic is a great candidate for recycling when compared to thermoset plastics such as epoxy, silicone, phenolic and polyurethane which burn rather than liquify.