Commercial Stainless Steel Alloys
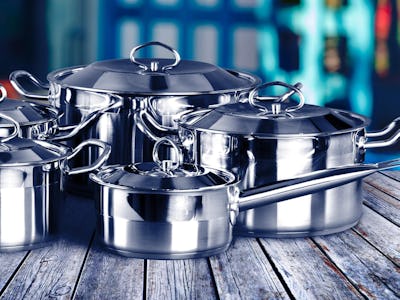
Righton Blackburns have been supplying the industry with stainless steel for over 100 years, building a reputation for quality and service with many customers in diverse market sectors.
Our range of stainless steel products includes long products, flat products, marine and aerospace materials, tubular products and handrailing.
Materials are sources from approved and highly reputable mills and our customers can have confidence that all materials supplied originate from trusted and proven manufacturers.
Our service centres around the UK and own fleet of delivery vehicles mean you can be sure that Righton Blackburns are able to handle your stainless steel supply needs reliably and consistently.
Stainless steel is available in a number of grades, which can be divided into five basic categories: austenitic, ferritic, duplex, martensitic, and precipitation Hardening.
Austenitic and ferritic grades are most commonly used, accounting for 95% of stainless steel applications, with type 1.4307 (304L) being the most commonly specified grade.
Probably the most common of the stainless steel categories, austenitic steels have high levels of chromium, with varying levels of other elements such as nickel, carbon, manganese and nitrogen.
These steels are divided into two categories, as determined by their additional alloys. Those with nickel form the 300 series, and those primarily using manganese and nitrogen are collectively known as the 200 series.
Practical applications for austenitic stainless steel include cutlery, kitchen appliances, surgical equipment and boat fittings, not to mention the structural composition of many components within the automotive and aerospace industries.
Also containing higher levels of chromium, ferritic steels, are the 400 grade steels. Noted for their magnetic properties, they also offer good tensile-property strength and ductility, and are highly resistant to thermal fatigue, corrosion and stress-corrosion cracking.
Ferritic stainless steel is tailored towards durability and are often found in automotive parts, appliances and throughout the catering industry.
The martensitic steels are also in the 400-grade series of stainless steels. They contain low to high carbon content, as well as chromium and 1% molybdenum. This is used when oxidation resistance and or corrosion resistance are needed coupled with either high strength at lower temperatures or creep resistance at higher temperatures. The martensitic steels have magnetic properties and possess good ductility and toughness and are easier to form.
Applications are broad and varied but include pump and valve parts, bolts, nuts and screws, surgical instruments, hand cutting tools and kitchen utensils, as well as parts for turbines and compressors.
Duplex stainless steels are a mixture of austenite and ferrite microstructures. They contain high levels of chromium and molybdenum, and exceptionally low nickel. This mixed structure gives this range of steels some very commercially attractive qualities, such as superb levels of toughness and corrosion resistance.
Placed in the 200 Grade series, duplex is ideal for the toughest of assignments, in the most demanding of environments. It is used for construction, cargo tanks, chemical plants and oil and gas processing, among many others.
Precipitation Hardening stainless steels are a collection of heat resistant alloys, which can be heat-treated to achieve extremely high tensile strength values, three to four times that of ordinary Austenitic steel.
This is achieved by adding aluminium, copper, molybdenum and titanium, either in mixed form or as individual elements.
Precipitation hardening stainless steels are widely used in the nuclear, oil, gas, and aerospace industries, where extreme tensile strength and corrosion resistance are the main required attributes.
The 200 Series chromium, nickel and magnesium alloys which use heavier amounts of manganese and nitrogen to limit the use of nickel. 200 Series stainless steels have 50% higher yield strength than the 300 Series due to the nitrogen element.
Content: Chromium, Manganese, Nickel, Alloys
The 300 Series are chromium and nickel alloys and by far the most used of the stainless steel variants
Content: Chromium, Nickel Alloys
Highly ductile and fast hardening. Great weldability and more resistant to wear than type 304
Slightly higher strength than 304 due to added carbon, and with equivalent corrosion resistance
This is an ‘easier to machine’ version of type 304, it gains this quality through added sulphur and phosphorus.
The most common grade of stainless steel - 18% chromium, 8% nickel baseline and the blueprint and comparison from which other steels are created.
Has better resistance to temperature than 304.
Behind 304, this is the second most common grade. It is commonly referred to as ‘marine grade’ due to a higher resistance to chloride corrosion than 304. The added element of molybdenum helps achieve this.
High heat resistance but with poor corrosion values, comprising 11% chromium and 8% nickel.
This is the cheapest stainless steel, made from iron and chromium.
High in strength and made from iron and chromium. Resistant to wear but with less corrosion resistance.
Martensitic ‘cutlery grade’. A distinct similarity to Brearley’s original stainless steel and excellent for polishing.
A decorative Stainless Steel in the ferritic family. Easy to form but lacking in resistance to corrosion and temperature.
Containing higher levels of carbon, this is one of the hardest stainless steels, it is essentially a higher grade of ‘cutlery steel’.
Heat-resisting chromium alloys, coupled with the 400 Series are the hardest of the stainless steels. Noted for being magnetic, they are hardened through a mix of both hard and cold working.
Precipitation hardening steels contain in the region of 17% chromium and 4% nickel content. When heat treated the PH Steel is hardened to a higher level than common martensitic alloys. The strength levels can be further increased with the addition niobium, copper and aluminium.
From catering to healthcare, automotive, aerospace and construction, it isn't too much to say that stainless steel has revolutionised the modern world, finding applications in almost every sector of manufacturing.
As a usable commercial material, stainless steel has outperformed aluminium, carbon steel and copper.
The secret to its commercial viability is in its exceptional physical and chemical properties, heat resistance of up to 1200c make it unique as a metal, as well as being weldable, easy to form and resistant to rust. It is also relatively inexpensive compared to other, non-corrosive alloys.
Over the past century, diligent work has continually been put into improving its techniques and processes, adding consistent quality and efficient manufacturing to a material with peerless properties.
Stainless steel is the name given to a widely used group of iron-based alloys. Noted for their high levels of heat and corrosion resistance, they are ideally suited to challenging environments, and industries where solid, dependable components are essential.
One of stainless steels main standout characteristics is its smaller chromium content, giving it superior corrosion resistance to other types of steel. It is primarily formed from iron and carbon but mixes in other elements such as chromium, molybdenum, nitrogen, nickel and magnesium.
Stainless Steel Properties
Stainless steel is considered a green product - it is non-degradable and therefore can be 100% recycled infinitely without any loss of its inherent qualities.
Steel is, therefore, one of the world’s most recycled materials and more steel is recycled each year than aluminium, glass, paper and plastic combined.
As a result, recycling stainless steel can result in a 95% reduction in the energy needed to reform the metal, as opposed to manufacturing from new materials. This means a significant reduction in the need to consume natural resources as part of its manufacture.
Stainless steel contains no toxic elements and therefore doesn’t cause issues with toxic run-off, making it an incredibly clean material for the environment. Indeed, the fact that stainless steel is non-toxic, easy to clean and resistant to bacterial longevity, is what makes it a primary source of material in catering, medicine and household appliances.
It is also highly resistant to other damages such as fire or water corrosion, giving it an even longer life expectancy, and creating much lower maintenance costs.
At just over 100 years old, stainless steel is a relative newcomer to the commercial metals market. Many previous attempts had been made to create steel that was resistant to rust, but none had succeeded until 1913 when Harry Brearley of Sheffield stumbled upon a mix of 12.8% chromium with molten iron and so, the first true ‘Rustless’ steel was produced.
Chromium was the key ingredient due to its corrosion resistance, and Brearley had happened upon this unique property while working for the British Army at the beginning of the First World War.
It was while he was trying to solve the problem of gun barrels eroding and chromium was the missing link.
After this discovery, improvements to stainless steel were inevitable and rapid. In 1919, Elwood Haynes from Portland, Indiana obtained the first patent on martensitic stainless steel, then in 1929 William J Kroll from Luxembourg discovered precipitation hardening stainless steel, and fast on the heels of that, duplex stainless steel came to the fore in the Avesta Ironworks of Sweden.
Experienced multi-product specialists
In-house state of the art processing facilities
Large fleet of bespoke delivery vehicles
Value-added services provider
Standard, non-standard and customer-specific material
Opening Times
Experienced multi-product specialists
In-house state of the art processing facilities
Large fleet of bespoke delivery vehicles
Opening Times