Introduction to Copper & Copper Alloy
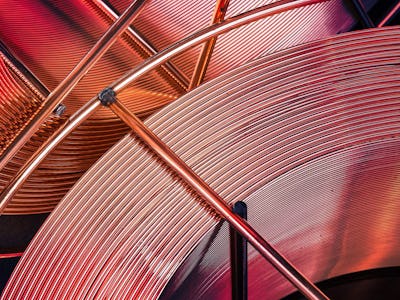
Copper is known for its electrical conductivity, corrosion resistance, heat transfer, structural capability and aesthetic appeal. Copper and copper alloys are amongst the most necessary materials needed to provide the means to keep homes, commerce and industry running.
Your search did not match any items. Please ensure all words are spelled correctly or try different / more general keywords.
All copper alloys resist corrosion by fresh water and steam. In most rural, marine and industrial atmospheres copper alloys are also resistant to corrosion. Copper is resistant to saline solutions, soils, non-oxidising minerals, organic acids and caustic solutions. Moist ammonia, halogens, sulphides, solutions containing ammonia ions and oxidising acids, like nitric acid, will attack copper. Copper alloys also have poor resistance to inorganic acids.
The corrosion resistance of copper alloys comes from the formation of adherent films on the material surface. These films are relatively impervious to corrosion therefore protecting the base metal from further attack.
Copper nickel alloys, aluminium brass, and aluminium bronzes demonstrate superior resistance to saltwater corrosion.
The electrical conductivity of copper is second only to silver. The conductivity of copper is 97% of the conductivity of Silver. Due to its much lower cost and greater abundance, Copper has traditionally been the standard material used for electricity transmission applications.
However, weight considerations mean that a large proportion of overhead high voltage power lines now use aluminium rather than copper. By weight, the conductivity of aluminium is around twice that of copper. The aluminium alloys used do have a low strength and need to be reinforced with a galvanised or aluminium coated high tensile steel wire in each strand.
Although additions of other elements will improve properties like strength, there will be some loss in electrical conductivity. As an example a 1% addition of cadmium can increase strength by 50%. However, this will result in a corresponding decrease in electrical conductivity of 15%.
Most copper alloys will develop a blue-green patina when exposed to the elements outdoors. Typical of this is the colour of the copper Statue of Liberty in New York. Some copper alloys will darken after prolonged exposure to the elements and take on a brown to black colour.
Lacquer coatings can be used to protect the surface and retain the original alloy colour. An acrylic coating with benzotriazole as an additive will last several years under most outdoor, abrasion-free conditions.
The yield point for copper alloys is not sharply defined. As a result it tends to be reported as either a 0.5% extension under load or as 0.2% offset.
Most commonly the 0.5% extension yield strength of annealed material registers as approximately one-third the tensile strength. Hardening by cold working means the material becomes less ductile, and yield strength approaches the tensile strength.
Highly prized in the marine industry the anti-microbial properties of copper make it resistant to bacteria, microbes and viruses. This is possible because of an outer layer or ‘Patina’ which is formed initially by corrosion but then acts as a protective barrier. This creates much fewer pathogens, and when alloyed with other metals it is the ideal choice for subsea conditions.
Expensive as a material compared to some other metals, copper requires less ongoing care and maintenance, making it a long term cost effective choice.
Containing no harmful compounds or chemicals, copper piping is a safe choice for the home or business. It is also highly recyclable so a kind choice for the environment.
Copper bar and sheeting is now often used in the construction industry for roofing and sidings. Found to be that much more resistant to the extremes of weather and temperature and able to last for up to 700 years thanks to its natural patina.
Copper bars also offer good conductivity to electrical demands, and are noted for appreciable flexibility, endurance and strength.
Used for centuries to transport drinking water, Copper is chemical free and safe to use in human environments.
As well as drinking water applications it has many other industrial uses, including home heating, solar energy, fire sprinklers, and air conditioning systems.
Another less known use of copper tubing is its applications in the gas industry. Applicable to standard gas or medical gas installations, it is able to meet exceptional safety standards.
Copper isn't permeable to gases or air, so will experience no leaks or contamination from outside the tube, and oxygen, temperature and UV rays do not alter its mechanical properties.
Copper wiring and plumbing is essential to home appliances that we use every day.
The largest end use for copper is in the building industry. Within the building industry the use of copper-based materials is broad. Construction industry related applications for Copper include:
In the automotive industry, copper is used for radiators, alternators, brake tubes and wring. Indeed, the average car contains 1.5 kilometres of copper wire with an average weight of 25 kilograms.
And the list isn't exhaustive - from hospitals to marine applications, oil and gas pipelines, shipbuilding and transportation, copper is an integral part of today's commerce and industry and a driving force behind new technologies and innovation.
The word ‘Copper’ derives from the old English ‘Coper’ which comes from the Latin phrase ‘Cyprium Aes’ whose literal translation is ‘Metal from Cyprus’.
Copper, as we now know it, is at the forefront of metallurgy, dating back as far as 8000 B.C.
Initially used for coins and ornaments, its recognition as an ideal material to make tools began at around 5500 B.C.
Between 4000 B.C. and 3000 B.C. it was realised that copper could also be extracted by heating copper sulphide Ore or ‘Blue Stones’.
This made copper more abundant and thus, much more used.
At around 3000 B.C. Bronze was discovered and man's transition from the Stone Age was complete.
Its early uses include cutlery, coins and tools, and other applications native to the country of origin, in China it was largely used for bells!
Copper was also used as a pigment, mixing with Azurite and Malachite to form blue and green tints, and then used decoratively for beads and Jewellery.
Another of copper's substantial benefits is its ease of re-use.
It can be limitlessly recycled without any loss of structural strength or integrity, allowing the possibility of multiple diverse applications.
it is estimated that around 40% of European copper use comes from recycled material, which is great news as the global demand for copper is ever increasing.
This also means it requires less extraction, reducing costs and the carbon footprint that Copper creates, and less harmful Co2 in the atmosphere.
The recycling rate for Free Machining Brass (CZ121/CW614N) is particularly high with clean/dry swarf having a high value, which contributes to the cost-benefit calculations in material selection.
Experienced multi-product specialists
In-house state of the art processing facilities
Large fleet of bespoke delivery vehicles
Value-added services provider
Standard, non-standard and customer-specific material
Opening Times
Experienced multi-product specialists
In-house state of the art processing facilities
Large fleet of bespoke delivery vehicles
Opening Times