Anti-Bacterial & Anti-Microbial Uses for Copper & Copper Alloys
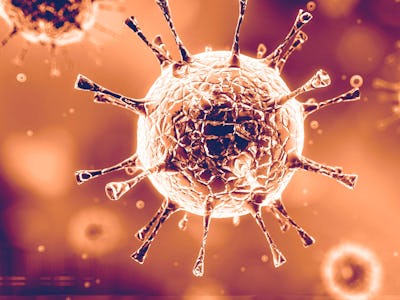
Available in both wrought and cast form, phosphor bronze and leaded bronze are used throughout many engineering industries and are ideal for heavy-duty components such as shafts, bearings and gears.
Leaded bronzes and gunmetals offer better machining characteristics than other bronzes while maintaining a good balance of corrosion resistance and strength.
Your search did not match any items. Please ensure all words are spelled correctly or try different / more general keywords.
Phosphor bronzes and tin bronzes are an alloy group with the primary content of copper, tin and phosphorous.
Usually, this balance is divided into 0.5 to 11% tin, and 0.01 to 0.35% phosphorous.
The tin element increases both the corrosion resistance and material strength of the alloy, while the phosphorous influence increases wear resistance and rigidity.
Phosphor bronze has excellent spring qualities, high resistance to fatigue, high corrosion resistance, and are superb to solder and form.
Primarily used in electricals, other uses can extend to spring washers and corrosion resistant bellows, bolts, bearings, dental bridges, ships propellers, and the reed components of organs and pipes.
The leaded phosphor bronzes combine this strength with high wear resistance, good thermal properties, substantial load-bearing capacity and better machinability, and are used for sleeve bearings, nuts, screws, electrical plugs and wiring, and doorknobs.
A phosphor bronze composition of 94.8% copper, 5% tin and 0.2% phosphorous is also used for cryogenic applications. Its combination of low thermal conductivity and electrical conductivity enables it to make electrical connections to devices at extremely low temperatures without adding heat.
Phosphor bronze sheets and plates are available in a range of thicknesses and are an ideal choice for welding projects.
Use is most common where wear resistance, high fatigue resistance, and superb forming characteristics are required such as electrical environments.
Cast bar is mostly used in electrical applications, but when continuously cast it can also be applied to decorative railings, furniture, springs, fasteners, and welding rods.
This process creates a densely structured alloy, free from blowholes and inclusions.
Superb mechanical properties make centrifugally cast rings an ideal production process for spigot bearings, rings, tubes, flanges and hollow cylindrical bars.
Continuous casting is a process whereby molten metal is placed into a mould that rapidly chills the metal to a solid state. This rapid cooling ensures a fine grain structure in the solid metal with higher performance characteristics than sand casting.
The cast shaped bar can then be cut as desired.
Phosphor Bronze grades PB1 and PB2 are both suitable materials for continuous casting.
PB1 has high mechanical strength, excellent corrosion and wear resistance and is an ideal choice for heavy loads
While PB2 contains higher tin and lower phosphor than PB1, it is suitable for heavy loading, as well as environments where high-sliding velocity and high-impact loading are essential.
Throughout the history of phosphor bronze there have been dedicated programs for the research and development of its capabilities and fine-tuning of its properties.
Much of this has been driven towards electrical connectors and switches because, while they performed well, they still lacked a crucial coveted property for electrical components - springiness in high-temperature environments.
A product was therefore still needed that could tick all the essential boxes of high electrical conductivity, strength retention at required temperatures, excellent inherent material strength, and yet still be easily fabricated to strip form while maintaining low-cost output.
So, experiments in making tiny changes to the structural composition began.
Around 2001, an alloy was developed at the Olin Corporation based in Clayton, Missouri, which could remove this final hurdle. They made two significant changes that ultimately provided the answers:
Its composition consisted of:
This composition created that springiness while retaining all its other ideal electrical characteristics, and also proved to be cheaper than initial phosphor bronzes.
So when we refer to ‘Phosphor Bronze’ today it is predominantly this newer version that has become the standard in electrical working.
Fascinatingly it is not strictly a phosphor bronze in the metallurgical sense, but more of an iron modification of tin brass.
Experienced multi-product specialists
In-house state of the art processing facilities
Large fleet of bespoke delivery vehicles
Value-added services provider
Standard, non-standard and customer-specific material
Opening Times
Experienced multi-product specialists
In-house state of the art processing facilities
Large fleet of bespoke delivery vehicles
Opening Times