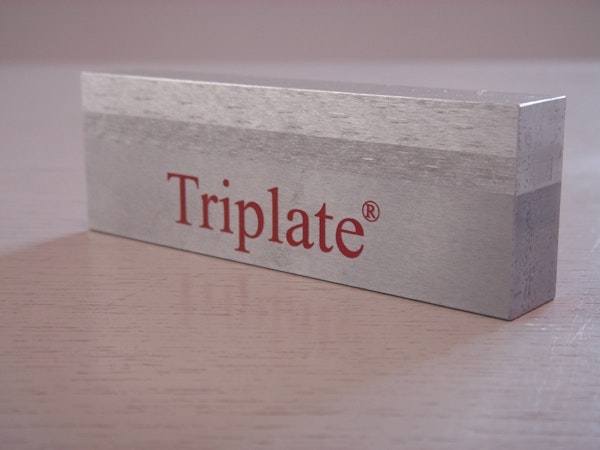
Dimension | Value |
---|---|
Standard strip width | Variable |
Standard strip length | max 3800mm |
Standard strip thickness - steel | 15 or 18mm |
Standard strip thickness - aluminium | 12 or 16mm |
Standard strip thickness - total | 27 or 34mm |
Range
Size (mm) | Comments |
---|---|
3800 x 16 x 34 | Triplate meets MIL-J-24445A and is approved by Lloyd’s Register of Shipping. |
3800 x 20 x 34 | 3.1 certification supplied unless requested otherwise. |
3800 x 25 x 34 | 3.2 Lloyds available upon request at time of production. |
3800 x 30 x 27 |
Whilst similar products are manufactured by explosive welding in atmospheric conditions, the unique shockwave process produces superior results as shown below.
Atmospheric vs Vacuum Cladding
Atmospheric | Vaccum |
---|---|
Coarse oxide agglomerations with porosity at the steel aluminium interface. | 100% dense, homogenous joint. |
Oxide agglomerations & porosity initiate fracture. | Does not apply. |
Oxide agglomerations & porosity can cause corrosion, in spite of protective coatings. | Does not apply. |
Bending of aluminium-steel strips can be difficult due to the coarser bond structure. | Very good formability due to ductile aluminium-steel joint. |
Production control is limited by variable weather conditions. | Optimal process control due to constantly reproducible vacuum conditions. |
Aluminium-steel joint is hard, making sawing & forming difficult. | Easy sawing & forming due to ductile aluminium-steel joint. |
Properties
Mechanical Properties
Property | Value |
---|---|
Shear strength – Basemetal/Intelayer | >55N/mm2 |
Tensile strength (through thickness) | 75N/mm2 |
Processing temperature | max 315oC |
Bend test base material in compression | Acceptable |
Bend test base material in tension | Acceptable |
Side Bend Test | Acceptable |
Chemical Composition
Layer | Material |
---|---|
Base material | Steel LRS Ship-Plate Grade A or St 52-/3N |
Interlayer | 99.5% pure aluminium - Alloy 1050A |
Superlayer | Aluminium alloy 5083 (AlMg4.5Mn) |
Processing
- During processing the temperature of the material MUST NOT be allowed to exceed 315°C.
- DO NOT pre-heat the transition joint before welding.
- Welding methods to be used are similar to those for the parent metals.
- Ideally the aluminium weld should be made first after removal of the aluminium oxide film by wire-brushing, followed by de-greasing. Argon shielding gas is recommended. Small diameter wires are recommended (1.2mm). Welding methods include GTAW, GMAW, TIG, MIG and Synergic pulse MIG.
- The steel weld is made using a coated electrode and GMAW, SMAW or FCAW. Small diameter electrodes are recommended (2.5mm).
- When bending ensure that the minimum bend radius is at least ten times the strip width or thickness.